There was once a time when human errors in manufacturing were difficult to address. This was due to the fact that at one point in time, there was minimal machinery. However, the times have changed, and manufacturing is now highly-dependent on advanced machinery.
As more and more machinery comes in to replace human labor, more and more human errors in manufacturing get noticed. It’s necessary for manufacturers to reduce human errors as these errors may lead to defects and failures in the products.
In this post, we’ll share some of the handiest tips with you so that you can reduce human errors in your manufacturing facility or plant. So, without any further delay, let’s get this post started.
1. Focus on the cause of the error
It’s easy to point fingers at individuals and lay the blame on them for getting things wrong. However, that doesn’t solve the problem, does it? Instead of playing the blame game, it’s better to delve deeper into the root cause of the error. For example, investigating a particular error may reveal that a worker was negligent. In this scenario, it would be alright if the authorities reprimanded the worker for negligence.
Errors may also be made by workers due to stress and being overworked. In this situation, it would be better to review the work conditions to see whether they’re responsible for causing the errors. If the investigations reveal that the fault lies with the work conditions, policies can be improved to ensure proper conditions for all workers.
2. Understand the difference between error and sabotage
When a wrongdoing is intentional with a motive of causing harm, it’s not an error – it’s sabotage. Simply put, errors are accidental, and many workers tend to make errors without thinking too much about the consequences of their actions. For example, a worker may perform a certain task with a particular expectation, and the results may be the exact opposite of what was expected.
When you understand the differences between an error and sabotage, you can approach the workers with the correct attitude. Instead of being too harsh towards them, you can use empathy to understand what made them perform the step that led to the error. You can also initiate training programs to ensure that similar errors don’t occur in the future.
3. Supervision is key
If there have been several instances of errors and mistakes even after thorough training, it indicates a lack of supervision. Supervising workers tends to improve workers’ performances as supervision keeps them on their toes and prevents them from committing silly mistakes.
Supervision is also a great way to distinguish between strong and weak performers. Through effective supervision, workers who are good at what they do can be rewarded. At the same time, those who repeatedly err and make mistakes can be trained for improving their performances.
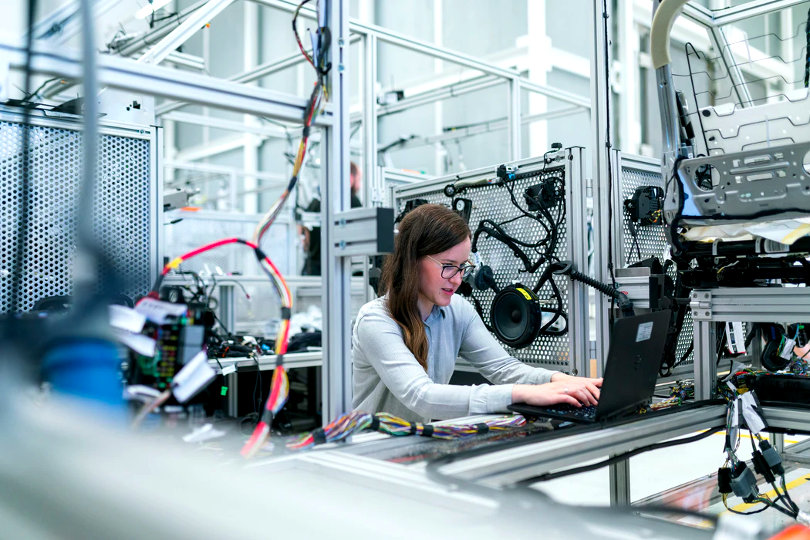
4. Improving work area design keeping human factors in mind
No matter how perfect a worker performs in a manufacturing facility, it’s not possible for someone to be 100% error-proof. Sooner or later, even the most error-free worker will make a mistake. That’s why it’s necessary to make improvements to the work area by keeping human factors in mind.
This will result in better working conditions for all workers, and also make it more difficult for them to make mistakes. For example, if the layout of your manufacturing facility is such that it leads to human errors, you should change it for the better.
5. Establish proper communication
Every manufacturing facility has different teams of workers who are all assigned different tasks to perform. If each team is solely focused on its own task, problems are very likely to occur. Instead, instructions should be passed down to each worker in a such a way that everyone is aware of not just their own tasks, but also of others’.
Communication should also be good between workers of different shifts. For example, the night shift should know the progress achieved by the day shift. This will lead to reduced wastage of time, with the night shift picking up exactly where the day shift left off.
Ultimately, you have to accept that human error can’t completely be eliminated. However, by putting these tips into practice, you can certainly reduce it.