The bill of materials (BOM) is an essential document that contains a wealth of information utilized in the production of a product. It is a detailed inventory that comprises a list of all the necessary materials required to manufacture an item, as well as instructions on how to assemble the product in the most efficient manner.
In essence, the bill of material serves as a comprehensive guide to the various components, raw materials, and guidelines required to manufacture, construct, or service a product. It is a vital component in the manufacturing process that ensures the smooth and efficient operation of the production line. If you wish to explore more about BOM, then keep reading!
What Is a Bill of Materials (BOM)?
A BOM is a document that contains a complete list of all the parts, components, assemblies, and other essential materials needed for the production of a product. Moreover, it provides guidance on how to acquire and utilize the materials listed.
Creating a BOM is a critical and indispensable step in the product development cycle. It is considered to be the foundation upon which various product development processes are built, providing a roadmap for the procurement and assembly of all the necessary materials and components. As such, it is imperative to create an accurate and detailed BOM to ensure the success of the entire manufacturing process.
What Are the Benefits of Using BOM?
Most manufacturing companies use a structured approach that includes a Bill of Materials (BOM) when planning and assembling their products. A bill of materials definition is a list of required materials for a project, including construction instructions, referred to as a Single-level BOM. Some of the most prominent benefits of bill of materials are written below. Let’s dig deep!
-
Simplifies the Intricate Production Structure
By breaking down the product into its component parts and providing a structured list of required materials, a Bill of Materials (BOM) simplifies the complex production process.
It allows manufacturers to manage their production and inventory process more efficiently by ensuring that all the necessary components are available at the right time and in the right quantity.
Additionally, a BOM helps to identify potential issues in the production process before they occur, enabling manufacturers to address them in a timely manner.
-
Ease of Progress From Designing To Assembling
The Bill of Materials (BOM) plays a critical role in simplifying the process of transitioning from design to assembly. By providing a structured list of required materials for a product, the BOM ensures that designers and engineers have a comprehensive understanding of the product’s components and materials, which can help streamline the entire design process and minimize the risk of errors.
Once the design phase is complete, the manufacturing BOM definition can be used to ensure that the necessary components and materials are available for production. This helps avoid unnecessary delays in the production process and ensures that the product is assembled efficiently.
-
Prevents Overspending
The use of a Bill of Materials (BOM) assists in controlling budgets by providing a detailed breakdown of the required materials for a product, along with their respective costs. This enables manufacturers to accurately estimate the total cost of production and establish a budget for the project.
This eventually prevents overspending by ensuring that manufacturers purchase only the necessary components and materials, reducing waste and increasing efficiency. As a result, cost savings can be achieved throughout the production process.
What Are the Types of Bills of Material?
Manufacturers create single-level or multi-level bills of materials (BOMs) to support various stages of the product development lifecycle. There are three main types of bill of materials: engineering, sales, and production, each of which serves a unique purpose and provides specific information necessary for the corresponding stage of the product development process.
BOMs are organized into different categories based on the information they contain and the purposes for which they are intended. They are created to support the unique requirements of each stage of the product development lifecycle. By using the right kind of BOM for each stage, manufacturers can streamline their operations and guarantee the success of their products.
-
Engineering Bill of Materials (EBOM)
In the product design phase, manufacturers create an engineering bill of materials (BOM) to define the original design of the finished product. This BOM includes all the parts, items, components, and subassemblies that are designated by engineering and are typically presented in the form of a technical drawing.
Creating the engineering BOM is the responsibility of engineers, who usually employ computer-aided design (CAD) software or comparable systems to ensure the accuracy and completeness of the BOM.
-
Manufacturing Bill of Materials (MBOM)
A manufacturing bill of materials (MBOM) is primarily used during the production phase to list all of the necessary components, assemblies, and packaging required to manufacture a shippable product while also accounting for the materials used during the manufacturing process, including waste.
This type of BOM provides a complete breakdown of the work required for each product component and groups the parts needed for each manufacturing stage, allowing personnel to determine when various manufacturing operations must commence and when supplies must be received to meet delivery deadlines.
-
Sales Bill of Materials (SBOM)
A sales bill of materials provides information about a product that is in the sales stage before its assembly. This type of BOM specifically includes details such as product specifications and features, but its structure is different from other BOM types and provides varying levels of detail.
The main objective of an SBOM is to easily manage a finished product as a sales item, helping businesses to effectively market and sell their products.
Who Prepares and Uses a Bill of Materials?
Typically, the engineering or manufacturing department is responsible for preparing the BOM. They are served with the responsibility of designing the product and determining the exact specifications of the necessary components before creating a list of materials required to create a bill of material.
Because of the essential pieces of information provided by the bill of materials meaning, it is utilized by multiple departments within a specific company. The purchasing department, for instance, utilizes the BOM to procure the required materials from suppliers by identifying the precise materials, quantity, and specifications that need to be met.
The production department and the inventory management department also utilize the BOM to ensure that all the required raw materials and components are available before the manufacturing process begins. The BOM assists them in assembling the product in the correct sequence and verifying that all the required components are present.
What Information Is Included in a BOM?
Below mentioned are the main components that a BOM contains. Let’s take a look at them!
-
BOM Level
By categorizing parts into different levels, we can gain a better understanding of all the components listed in the Bill of Materials.
Each level in the BOM is assigned a number or rank, which indicates its position within the BOM hierarchy. Depending on the complexity of the product, a BOM can be either a Single-level bill or a Multi-level BOM.
-
Part Number
Contract manufacturers assign this unique number to assist users in quickly identifying a part and its specifications without needing to refer to the complete specification. It’s essential to maintain consistency in numbering.
-
Part Name
A distinct identification is provided by the part name, which helps users recognize a component, much like the part number.
The stage of a part’s lifecycle, such as “in-production” or “in-design,” is indicated by this component.
-
Description
This particular component furnishes comprehensive information on a part or component that goes beyond what is provided by the part number or name.
Descriptions help distinguish between apparently identical components. For example, the term “screws” could denote a specific type of screw, such as machine screws that measure 1/2- and 5/8 inches in length.
-
Quantity
The number of components required for assembly is indicated by this element. For example, a piston cylinder may necessitate two piston rings.
-
Metric Units
This element specifies the unit of measurement used when purchasing and using a component to ensure that the correct amount is ordered. For example, wire is typically purchased in meters, while less expensive items may be procured by weight or by the box.
-
Type of Procurement
This details the method which is mainly used to acquire the part or component, such as cash, purchase order (PO), supply agreement, etc.
-
Referential Identifier
This is utilized in printed circuit-board assemblies primarily to identify the specific placement of each component on the circuit board.
-
BOM Notes
This element of the bill of material can be utilized to include additional information, like backup vendors or substance requirements, such as adhesive properties.
What Is the Bill of Material Format?
-
Single-Level BOM
A single-level bill of material lists every component required for the product once, along with the corresponding quantity needed, similar to a grocery list.
However, single-level BOMs are simple and do not show the interconnections between the various assemblies, subassemblies, and components that make up the final product.
As a result, diagnosing and repairing certain kinds of problems with the product can be a highly challenging task because it is not always clear which specific part or component is to blame.
-
Multi-Level BOM
A multi-level BOM, also called a parent-child BOM, provides a thorough understanding of the relationships and hierarchy between the various elements and sub-elements needed to develop a product.
The bill of material format is visually represented by the indentation of the parts and sub-parts that make up a higher-level assembly. Because of this, multi-level BOMs are also known as indented BOMs.
A multi-level BOM allows sub-assemblies to contain multiple components, and any modifications made to the parent assembly are also applied to the sub-assembly. This indicates that changes made at a higher level of the BOM will affect changes made at lower levels.
A multi-level BOM consequently offers a comprehensive and dynamic view of the product structure, allowing manufacturers to better manage their inventory and production process.
Wrapping Up
Creating and managing bill of materials definition manually can be difficult and prone to mistakes. But using software tools like inventory management software and supply chain management solutions can help make it easier.
Additionally, Enterprise Resource Planning (ERP) systems can help keep a constant track of changes to BOMs and spot errors that can happen when different teams create BOMs for the same product. With our highly experienced professionals, we can help you with the creation of your desired type of Bill of Materials with ease.
Connect with our experts today!
Frequently Asked Questions
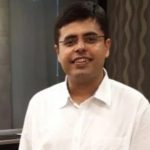
Amaey Anand is a certified accountant with over 10 years of experience in the finance industry. He has worked with various organizations to streamline their petty cash management processes and reduce inefficiencies. He has also written several articles on financial management for leading publications such as Zensuggest and The Wall Street Journal.
[adsanity_group align=’alignnone’ num_ads=1 num_columns=1 group_ids=’15192′]
Need Any Technology Assistance? Call Pursho @ 0731-6725516