A wide variety of human activities, which includes manufacturing, has taken its toll on the environment. While awareness regarding the environmental impact of these activities was limited in the past, it certainly isn’t limited today. Consumers around the world are waking up to the fact that unsustainable manufacturing is bad for the environment. As a result, more and more of them are choosing manufacturers that produce goods sustainably.
But what does it take for a manufacturing facility or plant to make the switch from unsustainable to sustainable? If you’re wondering what the answer is, read on. In this post, we’ll take you through some eco-friendly tips you can adopt to make sustainable manufacturing a reality.
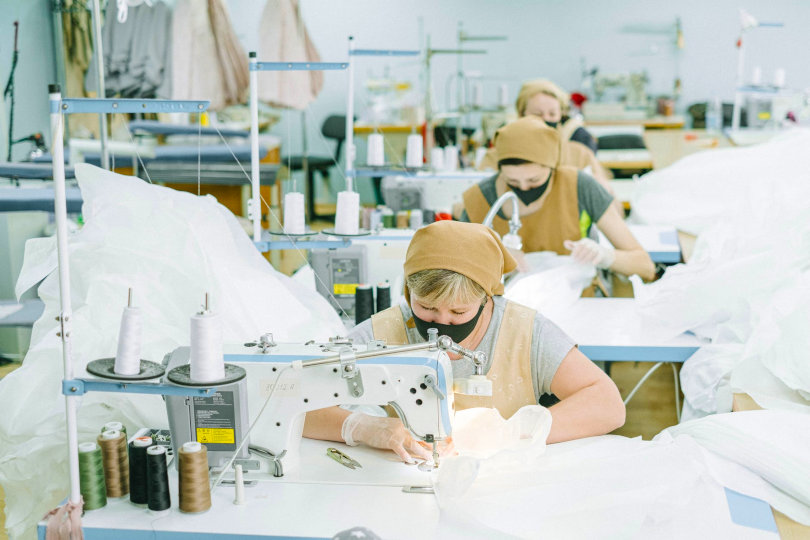
1. Start with Waste Minimization
Manufacturing hubs around the world have been singled out for criticism because of the huge volumes of waste they produce. If your plant has been guilty of the same, it’s time to put a few new practices in place.
For starters, keep a check on the stock of raw materials. Excess raw materials or resources tend to translate into waste, so it’s best to have just enough on-hand for producing a particular batch of products. You can order in more for the next batch after the previous stock has been exhausted.
For many manufacturing facilities, it’s tough to eliminate waste altogether. However, there are several techniques you can employ to make the most of the waste you produce. Filtration, centrifugation, reverse osmosis, and electrolysis are some of the most common techniques used by sustainable manufacturers.
You can also recover materials from waste by recycling it. Investing in a powerful industrial shredder is a great idea, as you can use it to reduce overall waste size. Industrial shredders can handle a variety of materials such as plastic, asphalt, rubber, wood, and more.
2. Pay Attention to Energy Consumption
The more energy your plant consumes, the more harm it does to the environment. That’s why it’s important to conduct energy audits from time to time. These audits will help you identify the systems in your manufacturing facility that are consuming the maximum energy. Once you know how much energy is being consumed, you should take steps to minimize energy consumption. There are several ways to do this.
The easiest is to upgrade the systems. For example, many manufacturing facilities around the world are still working with previous generation HVAC systems, which are inefficient compared to modern-day systems. So, upgrade all the older systems in place.
Systems may also consume more energy if they experience technical issues. So, ensure that repairs are performed regularly to keep all systems operating smoothly. And last but not the least, switch to energy-efficient LED lighting if you haven’t already.
3. Say No to Non-renewable Energy Sources
Wind, solar, geothermal, biomass, rain – these are all renewable sources of energy, and experts predict that the majority of the world will bank on them by 2035. Many countries around the world are offering tax incentives to manufacturers who are switching to renewable energy sources, so if you’re still reliant on non-renewable sources, it’s time to move on.
Non-renewable sources like fossil fuel are naturally-produced. However, their natural production is a process that takes place over thousands of years, which makes it impossible for them to cater to the ever-growing human demand. Generating electricity from these sources also increases carbon emissions, which results in an increase in global temperatures.
The effects of climate change are already on display in the form of melting glaciers, high-intensity natural disasters, and unnatural seasonal changes and weather patterns. Don’t make it worse by continuing to rely on non-renewable sources of energy.
This infographic was created by Keyence, a provider of optical profilometers
4. Purchase Raw Materials from Local Sources
Raw material transportation adds to the manufacturing sector’s carbon footprint. That’s why it’s best to try and source raw materials locally. Local raw material sourcing is beneficial not only for reducing your factory’s carbon footprint. It’s also about supporting the local economy, which will ultimately help local communities to prosper.
Of course, it will take some time for you to put all these changes in places. But the sooner you get started, the better it will be for all involved – your facility and its profitability, your customers, and most importantly, the environment.